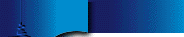
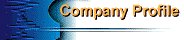
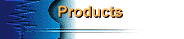
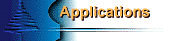
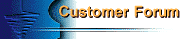
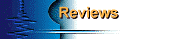
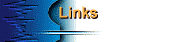
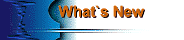
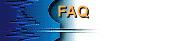
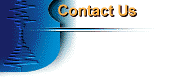
|

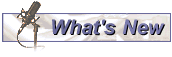
Spot Weld Inspection in the Automotive Industry:
ScanMaster's new computerized spot-weld inspection system has been in operation with the leading automotive companies.
The current method in the industry is to test the spot weld using the chisel and hammer method accompanied by visual inspection. This method takes time and the part often requires rework or is often discarded.
Testing to destruction of car sub-assemblies and/or complete car bodies in three of the United States' biggest car manufacturing plants costs an estimated $400 to $600 million per year through loss of value-added inventory.
If 50% of the components including spot welds could be tested non-destructively and then sold, the potential cost saving could be approximately $200 to $300 million per year.
Reducing by 10% the number of redundant welds in a car may yield savings of $400 to $600 million/year.
Other non-destructive testing methods have been tried for inspecting spot welds, but most of these fail to reliably detect "stick" or "cladding" type spot weld defects. These methods include: thermal/infrared, electrical conductivity, x-ray and eddy current methods.
The ultrasonic method is fast, "stick" welds can be detected and automated classification allows inspection of production line spot welds in an efficient and reliable manner.
|
| Chisel and hammer |
Destructive | UT |
Cost/car($) |
5,150 |
7,270 |
1,210 |
Detection (%) |
20 |
99 |
95 |
Cost comparison
|
The upi-50/SW ultrasonic instrument and the associated algorithm provide a method for operator-independent decision making and classification of defective spot welds during production.
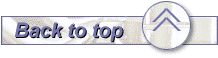
| |