Historical overview of
pile integrity control by the reflection and impedance methods
at CEBTP :
Three men, Jean PAQUET, from CEBTP,
along with his team, Jean-Pierre CHIPART, Michel BRIARD and
André CABÉ are the authors of pile controlling
by the echo, vibratory and pulse method.
Using a method of echo detection for pile
control was first contemplated at CEBTP in 1964.
1965 :
The first trials to control the continuity of piles
by the echo method took place. The prompting to the pile
was provided by four magnetostrictive hammers. The signals
were collected by five acceleration sensors. Measurements
were made on real piles located at Porcheville, in France.
Trials
were also made on replicas of piles made of AFCODUR polymer
material, with a diameter of 50 mm, in order to refine the
method.
|
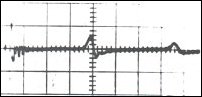 |
1966 :By
the time, the impedance method was called vibratory method
or mechanical admittance method. It was already used in
aeronautical structures, but the difficulty lied in applying
this method to piles in buildings. A more important energy
was indeed required, whereas lower frequencies were also
to use.
|
|
The first technique consisted
in fitting the top of the pile with a prompter using a vibrating
cylinder. One therefore had to bind this cylinder to the
pile, and be certain the cylinder was aligned with the axis
of the foundation. To achieve this, a crown shaped rubber
mould was set onto the top of the pile, and a resin was
cast inside. After drying, a perfectly plane and horizontal
surface was available. A plate with a force sensor was placed
between the vibrating cylinder and the resin. Oil enabled
to have a good contact between the different elements. A
geophone (a HALL SEARS H.S.J. minute seismograph) fastened
between the whole set collected the response of the pile.
|
|
The pile was prompted by the
vibrating cylinder by means of a frequency ramp went from
3 Hz up to 1000 Hz.
The velocity collected by the geophone and the force collected
by the force sensor were recorded, and the velocity to force
ratio allowed to plot the curve of mechanical admittance
versus frequency.
One could then get to know
the length of the pile, but also its suppleness and its
characteristic admittance.
|
|
1967
: The prompting of the pile by means of a magnetostrictive
hammer was left away and replaced by a simple hammer fitted by
a trigger. This allowed to apply the echo method. The velocity
signal was collected by a single sensor of the HALL SEARS type.
1972
: The prompting with a vibrating cylinder was abandoned
and replaced by a hammer which strikes the pile through
a KISLER quartz force sensor.
The vibratory speed was sensed by a HALL-SEARS 4.5 Hz
geophone.
This technique allowed to obtain
the harmonic and the pulse responses at the same time (echo
method).
|
|
1977 :
A HEWLETT-PACKARD 21 MX computer was first used, whose programme,
developed on purpose, was stored on a punched paper tape (the
memory capacity was 16 Kbites). The force signal was measured
by a SEDEME CC 10 force sensor.
1979
: Birth of the MIMP 11 equipment, based on a LS 11 computer
of DIGITAL EQUIPMENT.
For the first models, the result was plotted by a recorded
with a step by step engine ; it was plotted by an X-Y analogical
plotter for the further models.
The MIMP 11was the equipment
on which a hammer directly fitted with PCB brand force sensor
was used.
|
|
1986
: The MIMP 12 equipment was issued, based on a GRID
CASE brand computer. The data were stored on a diskette.
|
|
1989 :
The MIMP 14 equipment was developed, not to test piles, but to
detect voids behind the voussoirs of the tunnel under the English
Channel. The MIMP 14 was based on a PC 286 microprocessor, and
on a DATA TRANSLATION brand acquisition card.
1990
: Issue of the MIMP 15 material, first based on a PC
286, then on a PC 486. The acquisition card was especially
designed by CEBTP.
|
|
1991
: Creation of the IMPRO software, allowing to build up the
impedance profile of a pile.
1998
: The MIMP 16 material, which is the last generation
of a long series of MIMPs, is a large step forward.
It displays advanced performances,
it is small, it has a light weight, and it can store as
many as 1000 signals in its internal memory.
The MIMP 16 material allows
to operate the reflection or impedance pile control method
as well as to apply the void detection method under pavings,
voussoirs, cemented façade panels, or large pipes.
|
|
Moreover, the MIMP 16 material
offers an outstanding pile integrity data processing software
called IMPRO2 (under WINDOWS 95 or 98).
|
|
|